|
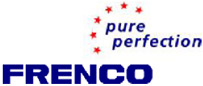 |
|
|
|
Rotation inspection instrument with ball URM-K |
|
|
|
The URM-K measuring instrument is a very flexible device to inspect profiled components, such as profiled shafts. The traditional place for the unit to be used is on the shop floor directly next to the production machine. This location is ideal for quick and reliable sampling inspections. |
|
|
|
Criteria and Applications : |
|
-
Quick and precise determination of gearing features such as dimension, concentricity, roundness, individual and cumulative pitch deviation, helix angle.
-
Easy operation.
-
Diameter inspection for size, concentricity and roundness.
-
Determination of locational deviations by referencing the gearing, diameters and surfaces.
-
Highest precision by means of substitution method (calibration on setting masters).
-
Flexible and versatile for use with all types of different workpieces.
-
Simultaneous visualisation of size, form and locational deviation.
-
Link between production and inspection room.
-
Very robust design, to be used on shop floor directly next to the machine tool.
-
Minimum maintenance costs due to its excellent wear resistant design.
-
Documentation of the measuring results for process control, e.g. QS-Stat® interface.
-
Customer specific adaptations of mechanics and software.
-
Interlinked usage within automation possible.
|
|
|
|
Types : |
|
The URM-K is available with different options. Choosing the right instrument depends on the workpiece to be measured and on the measuring task. All instruments can be driven manually, semi-automatically or fully automatically. We are happy to advise you on and supply you with tailor-made instruments for your requirements.
The following are examples of measuring task and measuring geometries already implemented: |
|
|
|
|
|
Software: |
|
The design of the URM-K software is very functional. All required information is clearly laid out on the graphical display. This enables the operator to identify the current measuring location easily and whether the workpiece has passed the inspection or not. |
|
|
|
|
|
Interfaces for databases and QS-Stat® are available. |
|
|
|
Rotation inspection instrument with wheel URM-R |
|
|
|
The inspection instrument URM-R is most suitable for fast 100% inspections of profiled components, such as toothed shafts. The workpiece is held between two centres – it rotates by 360 degrees during the inspection process – and different inspections can be carried out simultaneously, e.g. splines, bevel gears, spur gears, diameters and plane surfaces. The traditional place for the unit to be used is on the shop floor directly next to the production machine. This location is ideal for quick 100% inspections. |
|
|
|
Criteria and Applications:
-
Quick and prices determination of gearing features such as dimension, concentricity, roundness, individual and cumulative pitch deviation, helix angle.
-
Easy operation.
-
Inspections of splines, bevel gears, spur gears, diameter and surfaces.
-
Diameter inspection for size, concentricity and roundness.
-
Inspection of several simultaneous measuring points.
-
Determination of locational deviations on gearing, diameter and surfaces.
-
Ideal for 100% inspection on the shop floor.
-
Reducing the workload of the inspection room.
-
Documentation of the measuring results for process control, e.g. QS-Stat® interface.
-
Highest precision with substitution method (calibration with setting masters).
-
Customer specific adaptations of mechanics and software.
|
|
|
Types: |
|
The URM-K is available with different options. Choosing the right instrument depends on the workpiece to be measured and on the measuring task. The instruments can be driven either semi-automatically or fully automatically. We are happy to advise you on and supply you with tailor-made instruments made to your requirements.
The following are examples of measuring task and measuring geometries already implemented: |
|
|
|
|
|
|
|
Software: |
|
The design of the URM-R software is very functional. All required information is clearly laid out, which enables the operator to identify whether the workpiece has passed the inspection or not at a glance. Interfaces for databases and QS-Stat® are available. |
|
|
|
|
|
|
|
Double Flank Gear Rolling Inspection URM-WZ
|
|
|
|
|
The double flank gear rolling inspection is an easy and quick inspection method for gears. The inspection process can be carried out on the shop floor. It immediately enables the user to evaluate gears with regard to the total errors caused in production.
The double flank gear rolling inspection is, if used with modern evaluation equipment such as a PC, hardware and software, a very efficient and quick way of ensuring quality without any problems. Below is a selection of typical workpieces: |
|
|
|
|
Measured values and evaluation:
The basic principle of the double flank gear rolling inspection is based on a master gear (a near perfect gear) and a gear (= workpiece) are in rolling contact, free from backlash. The inspection instrument has one rotational axis which is fixed and one which is movable. The centre distance variations during the rolling process are caused by form errors on the workpiece and are the basis for the evaluation of the inspection. In the following are the individual inspection parameters in more detail: |
Double flank radial error Fi'': is the fluctuation of the centre distance a'', i.e. Fi'' is the difference between the largest and the smallest centre distance a'' within one revolution of the inspected gear (DIN 3960 / 3963).
Cause: All gear errors can influence the result.
|
Double flank tooth-to-tooth deviation fi'': is the largest difference in the centre distance a'' that occurs within an angle of rotation corresponding to the engagement of one tooth (DIN 3960 / 3963).
Cause: Errors in certain tooth segments or in individual teeth.
|
Double flank runout deviation Fr'': is the long wave-length component of the double flank composite error. It is obtained by drawing a “mean line” into the test diagram of the double flank gear rolling inspection, whereby the short wave-length components are suppressed. The runout deviation Fr'' is therefore the distance between the highest and lowest point of the mean line (DIN 3960 / 3963).
Cause: Eccentricity of the gearing in the measuring plane perpendicular to the centre line of the gear, and by non-uniform space widths caused by pitch deviation.
|
Short wave-length component fk'': is accrued from the difference between the recorded test diagram lines of the gear roll error Fi'' and the ‘mean line’ of the runout deviation Fr''
Cause: Waviness in the profile deviations and flank line deviations will have an influence.
|
|
|
|
|
|
|
|
|
Advantages of Frenco double flank gear rolling testers:
-
Solid and robust design for use on shop floor.
-
Simple, yet very stable component design.
-
True modular design.
-
The double flank gear roll testers can be constructed to customer-specific requirements and made to suit the test items and test conditions due to the variety of modular design components.
-
The measuring instruments can be up-graded and expanded at any time.
-
Measuring force progressively adjustable.
-
Quick release of the measuring slide.
-
Fixed centres and arbours on measuring slide, adjusting slide or machine bed, which eliminates any influences of runout deviation of the mounting. attachment. The gear, mounted on the drive side of the measuring slide, is driven by a special driving device.
|
|
|
|
Single flank Gear Rolling Inspection URM-WE
|
|
|
|
The most popular and widely-used inspection method for gears is currently the double flank gear rolling inspection. However, the more realistic, i.e. closer to the gear’s actual operating conditions (e.g. in a gearbox), inspection method is by using the single flank gear rolling inspection where both workpiece and master gear are at a fixed centre distance. The right and left flanks of the workpiece are inspected by single flank contact of the master gear. Any changes in the angle of rotation are identified during this inspection process. |
|
|
|
|
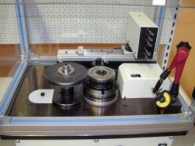 |
Traditional layout of a single flank gear rolling inspection |
|
|
|
|
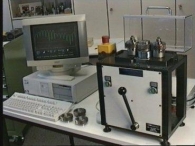 |
In this layout, all right and left
gear flanks are inspected simultaneously
(middle: workpiece,
right / left: a master gear each). |
|
|
|
|
Evaluation is done by identifying the deviation of the measured angle to the angle of rotation, from which the given tolerances as per DIN 3960 and 3963 – right hand and left hand flank – can be calculated for:
- the single flank radial composite error Fi',
- the single flank tooth-to-tooth deviation fi',
- the runout deviation Fr' and
- the short wave-length component. |
|
|
|
Comprehensive evaluations are possible with this software and they can also be customised to your own requirements. |
|
|
|
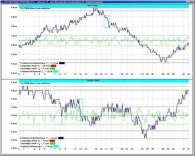 |
Typical graph
top window: evaluation left flank
lower window: evaluation right flank |
|
|
|
|
Roll Scan Inspection URM-WS
|
|
|
|
Roll scan inspection means that gears are scanned in rolling contact with a special inspection gear. The instrument combines the simple, robust and temperature stable design of the single flank gear rolling inspection with the greatest information density of modern coordination measuring technology, yet the measuring time remains short. |
|
|
|
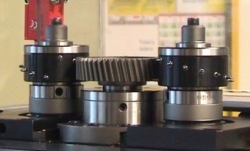 |
Roll master with involute-like
measuring pins in alternating planes |
|
|
|
|
Using special pins in the inspection gears ensures a metrological favourable and thin line of contact with the workpiece. Several section planes on all flanks are measured during inspection. A complete topography of the gear flanks is then calculated from the sections. |
|
|
|
|
|
100,000 measuring points can be taken within 2 minutes.
This creates a measuring point grid on the gearing.
|
|
|
|
The evaluation software enables the user to view conventional charts but also modern area analyses and tolerance analyses on all gear flanks. |
|
|
|
|